Harmonized 3-nozzle linking powers fully automated production
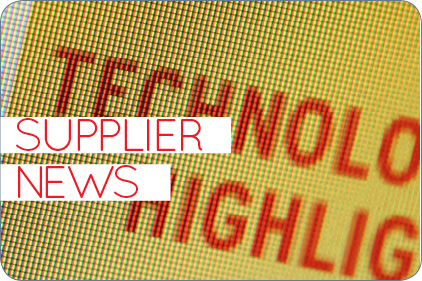
Handtmann’s new fully automated revolving 3-nozzle PVLH 246 and PVLS 143 AL systems offer approximately 1.7 second automatic casing changes with gentler portioning, less rework and the industry’s most efficient linking and hanging performance.
According to Tom Kittle, president of Handtmann Inc. and Handtmann Canada Ltd., “our new AL systems bring a dramatically new level of efficiency to fresh, cooked or dry sausage production in natural, artificial and collagen casings by more intelligently filling and handling linked or separated sausages and portioning them to one gram accuracy.”
Many of the minor hygienic and ergonomic issues that are problematic with other multi-horn systems have been resolved, making a big difference in total performance. For instance, the new AL casing loading mechanics operate with fewer moving parts for less wear, easier cleaning, and improved hygiene. These new Handtmann AL systems now automatically wipe sausage meat from each nozzle so it cannot fall on the slug in the filling position. They spool slugs immediately before the change to reduce troublesome humidity absorption and each nozzle is positioned at the loading stage for “no leaning” operator access. Operator flexibility also helps optimize change times. Nozzles can be returned to the filling position and restart occurs with a simple hand movement that eliminates any swivelling procedure.
The redesigned automatic casing loading system gives processors the flexibility to manually load natural casings when needed and automatically load collagen and artificial casings. Handtmann’s new advanced nozzle-centering function stabilizes the horn and more precisely guides the casing to make larger nozzles possible and recalibrate virtually error-free spooling as the new industry norm.
Highly dynamic Handtmann linking now also automatically adapts to each product for more consistent quality, more attractive ends, and fewer casing bursts no matter the casing type.
In addition, short set up times and the ability to process curved collagen casings combine with the proven flexibility of Handtmann VF stuffers to dramatically increase the range of linking and hanging products now achievable with a single system. Handtmann’s technical advancements in these models let them efficiently adapt to even slight product variations, optimizing the transfer of product to the hanging unit regardless weight, length and loop specification. Freely definable hook groups are only offered by Handtmann, simplifying easy removal with better ergonomics and faster loading into smoking systems or other downstream processes.
“Our new state-of-the-art technology harmonizes AL functions with the quickest casing change times, most precise weights, and most error-free processing that is available,” says Kittle.
“We think this AL series is built on major technical advancements that will move AL processing to a new level and that our new system control advancements in combination with the new PVLH 246 and PVLS 143 production platforms will continue redefining performance standards well into the future.
“The proof of our Handtmann performance has always been most visible in our customers’ products. And the proof of our new AL equipment’s revolutionary value will be in the reliably precise performance it delivers with ever changing products for many years to come.”
Handtmann specializes in best-of-breed portioning and linking equipment, providing practical value with efficient technology and services for filling lines and processing businesses. Handtmann Inc. and Handtmann Canada Ltd. are North American wholly owned subsidiaries of Albert Handtmann Maschinenfabrik GmbH, a leading global technology solutions provider to the food processing industry. The Handtmann group is a family owned business established in 1873 and headquartered in Biberach, Germany. www.handtmann.us
Looking for a reprint of this article?
From high-res PDFs to custom plaques, order your copy today!