Films and Barriers
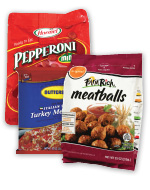
Keeping it safe and easy
With the unexpected and unfortunate advent of Listeria monocytogenes in processed-meat packages, processors scrambled to find a process to exterminate the invader and preserve food quality. Most began using post-pasteurization, but existing materials could not withstand the brief exposure to higher heats. However, flexible-packaging suppliers moved quickly to fill the gap.
Meeting consumer needs for more convenience will be a constant challenge for processors. Products need to be easy to access, store and prepare, especially as household size continues to shrink and food preparation time decreases.
With tear strips, easy-to-peel seals, zippers and other devices available for many years, the processor has many options. While many of these work beautifully, some inevitably fail. How many of us as consumers have had tear strips not tear as intended, easy-peel seals requiring the strength of Hercules, or zippers tear away uselessly from the package?
Suppliers continue to work on improvements to these systems. Most recently, recloseable meat packages have been introduced that eliminate the extra cost, machinery and processing requirements for adding a zipper. These systems, available from multiple vendors, use special sealing adhesives that provide a hermetic seal for distribution, yet can be resealed by the consumer for storage.

The newest, and possibly most far-reaching demands are the sustainability initiatives of Wal-Mart, ConAgra and many other retailers and processors. On top of the requirements for product safety and convenience, packages must reduce their environmental footprint.
Sustainability goes far beyond the 1990s mantra of reduce, recycle, reuse” although these remain very important. Wal-Mart and others have developed scorecards to measure carbon dioxide production, cube utilization, transport distance, renewable energy and many other items relating to packaging of meat and other products.
However, flexible packaging will have an advantage on most of these measures, since it is very compact to transport and adds very little cost to the product compared with other forms of packaging. Yet it likely will face challenges in the recycling arena, since it contains multiple components that are difficult to reuse. In addition, inks and adhesives that contain heavy metals or volatile organic compounds will be under scrutiny.
Whether for the basic requirements of product protection and food safety, consumer convenience needs or more complex sustainability initiatives, flexible packaging will continue to meet the stringent demands of the meat industry.
Huston Keith is principal of Keymark Associates, a market research and business development firm in Marietta, Ga. (www.keymark.net). He is also a member of The National Provisioner’s Editorial Board and can be reached at (770) 579-5979.
Looking for a reprint of this article?
From high-res PDFs to custom plaques, order your copy today!