Beef plant of the future
Smaller operations, improved technology, more automation expected
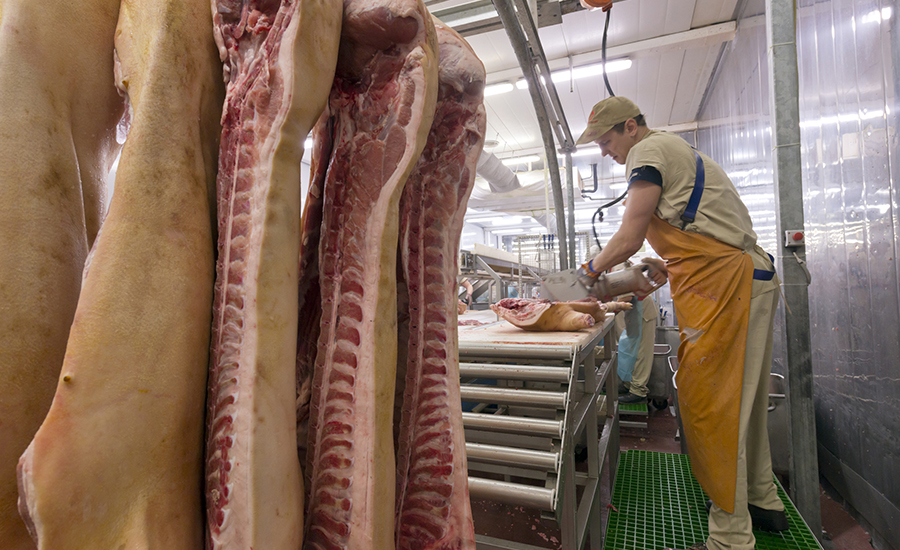
The introduction of COVID-19 caused unexpected changes for the world and will continue to have an impact on the agriculture industry for years to come. One of the industry segments directly hit by this change will be the beef packing segment.
Many of the changes began well before COVID but were accelerated as a response to pandemic-induced circumstances. In reality, a crystal ball might be necessary to reveal exactly how the beef harvesting and processing plants of the future will look. Five years ago, industry leaders might have asked how beef processing would change in 10 to 20 years. But now, given how extensively the tides of change have affected the meat packing industry, today’s agricultural leaders should be asking what beef plants might look like in as little as five years.
The United States has fewer than 30 large plants that harvest more than 85% of our fed beef. These plants are old, have large hourly work forces and fight a continuous battle to upgrade and incorporate modern technologies within existing space/configuration limitations.
What to consider for the next phase of beef plants
Several questions need to be considered for what’s to come. What changes should the beef packing industry expect in the next five years? How many cattle will the new plants harvest each day? What type of workforce will be utilized? How will robotics and other technologies be utilized?
After polling several industry leaders and experts, the following are some beef processing expectations:
• New beef plants will be smaller and will harvest fewer than 2,000 head per day.
• Cattle will be sourced from the ranch, stocker and feeder and will be selected to be more consistent in weight, frame and type to meet specific branded product needs.
• Cattle handling pens will continue to be designed with animal welfare as a priority.
• Block chain technology will be enabled to allow transparency and traceability of product moving from the ranch to the finished package.
• The design of the plant of the future will likely begin by looking at the technology currently being used by the pork industry. First steps could be to modify or automate existing technology for beef carcass splitting, evisceration and foot and head removal.
• The plant of the future will likely begin the slaughter process with chemical dehairing on the harvest floor, a major intervention to control bacterial growth on the carcass. Dehairing will produce a clean carcass that has been commercially sterilized on the surface. Little to no surface trimming will be necessary, thus increasing yield and decreasing the need for trimmers.
• Cattle will be handled on the harvest floor in a different manner. The packing industry will utilize automated hot fat trimming of surface fat, allowing for decreased labor in the fabrication room and more uniform chill. The packing process will also include partial hot boning of parts of the carcass. These hot-boned products will go straight into value-added products without chilling. Product yields will be significantly increased.
• Robotics will have expanded roles throughout the plant. Many feel that robotics will see expansion in the fabrication and value-added areas, but robotic technologies could also be effectively utilized on the harvest floor. Hourly jobs will decrease or change significantly, but IT-type jobs will increase. Processing steps require intensive worker involvement. Ideally, technology will assist in those processes and make those jobs safer and less strenuous, resulting in better precision, less worker fatigue and less variable products.
• Worker safety will be improved by using robotics in the more difficult or dangerous jobs.
• Artificial intelligence and machine learning will be used in every step, from the ranch to the finished package.
• The plant of the future will be digitized. All data will be captured digitally so that real-time monitoring of worker safety, food safety, etc. will be possible. Issues will be tracked and addressed before the product leaves the plant. All paper will be removed from the food processing floors.
• The plant of the future will have different layouts in deboning areas to accommodate the use of new robotic systems.
• Trim will be handled more efficiently, resulting in better lean-point management.
• The plant of the future will have the ability to capture better yield data due to the in-line carcass identification coupled with robotics that necessitates in-line processing. True carcass yields will drive improvement.
• The plant of the future will have streamlined and automated packaging systems resulting in reduced labor and packaging costs.
• Vision technology coupled with artificial intelligence, bio-metrics and machine learning will create strong management operating systems that allow for real-time feedback on things such as employee safety, food safety, sanitizing procedures, labor efficiency, adherence to job procedures, social distancing and yield management.
• Use of camera systems will be expanded throughout the plant to measure animal handling, product workmanship and worker safety.
• The plant of the future will be more focused on supply chain and consumer claims, which better link the producer to the consumer.
• With chemical dehairing and the removal of dirt, hair and their associated pathogens, the slaughter process will produce a more even hide split and a higher yield of raw materials for pet treats.
• Airflow in the plant will be clean to dirty.
• Improved water-use systems will decrease overall use and increase water reuse.
• The newer plants will generate much of their own energy needs from biodigesters.
• The plant of the future will be a total food plant that produces not only boxed beef, but value-added products such as retail case-ready products, sous vide cooked products, snack foods and pet treats.
• All of these new technologies will drive new challenges to recruit and train highly skilled labor to rural locations.
These changes may be accomplished in five years or less. In 10 to 20 years, the harvesting segment of the beef industry will likely be taking even greater leaps than those suggested, through incorporation of technologies not yet on the market. It is possible that the plants of the future will have the capability to harvest and fabricate 2,000 animals per day with 80% fewer hourly workers, changing the face the harvesting industry.
Looking for a reprint of this article?
From high-res PDFs to custom plaques, order your copy today!