Tech | Packaging
Chubs tick boxes on packaging wish list
Flexible packaging format appeals to consumers, retailers and processors.
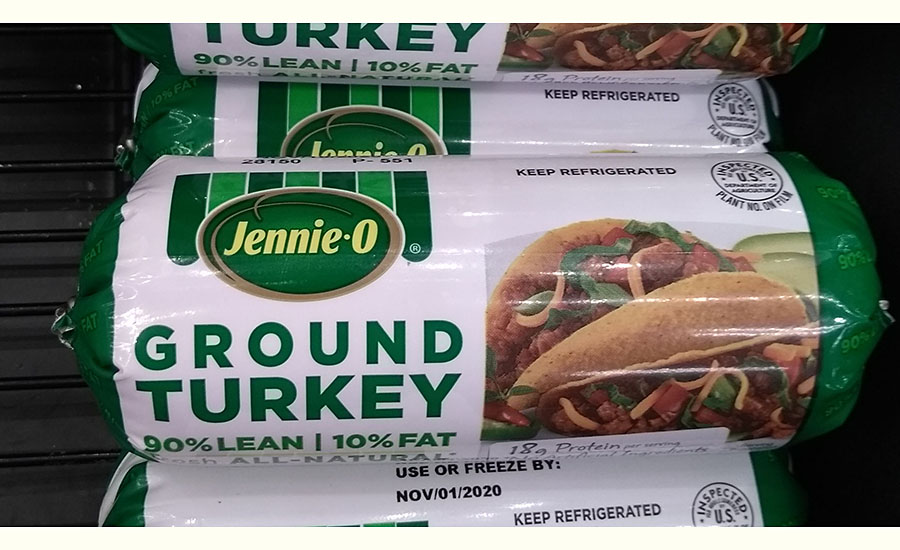
When a processor makes a packaging wish list, chub packaging ticks most of the boxes. Sustainable? Yes. Case-ready? Yes. Vibrant, full-color graphics? Yes. Potential for portion control? Yes. Extended shelf life? Yes. Freezer-compatible? Yes. Convenient? Yes. Economical price points? Yes. Easy to stock? Yes. Relatively low-cost equipment and consumables? Yes. Low barrier to entry? Yes.
Consumers, foodservice providers and retailers like the format for many of the same reasons. Applications include virtually any pumpable cooked or fresh meat including ground beef, ground turkey, sausage, chorizo, salami, taco meat and pet food.
Processors can select from a wide range of equipment from semi-automatic tabletop units to fully automated machines to produce one-, two-, three-, five-, 10- and 20-pound chubs. Vertical form-fill-seal machines are commonly used, and speeds range from 15 to 160 chubs per minute, applying clips that are pre-formed or formed online from rollstock. Machines run flat film and rely on high-frequency, hot-air, extrusion or cold sealing. Online clip forming generally offers some cost savings. Like many of today’s packaging machines, chub equipment often combines advanced electronics and software to simplify operation and maximize flexibility and connectivity to other systems. Washdown-compatible machines are designed to be easy to clean and sanitize. Changeover time can be 15 minutes or less.
For higher-volume operations, robotic systems can eliminate manual case loading. Quality control systems such as X-ray inspectors and metal detectors prevent contaminants in finished products. X-ray systems also can provide inline fat measurement and reject any product that is incomplete, flawed or outside weight tolerances.
Chub film can be clear, white or printed for maximum shelf impact and compatible with hot or cold filling. Multilayer structures based on nylon, polyethylene or polyethylene terephthalate provide puncture resistance and good sealability and protect product shelf life. Incorporating a barrier layer such as polyvinylidene chloride can extend shelf life and offers the opportunity to reduce food waste and expand distribution to a larger geographic area. For example, chub packaging for Our Certified brand ground beef from Cargill offers up to 21 days of refrigerated shelf life. Unopened chubs may be frozen for up to six months without any additional packaging. Surface or reverse printing can reproduce full-color graphics for maximum shelf impact and product differentiation. Cargill, for example, uses color coding to make it easy to identify the desired lean-to-fat ratio among the seven lean points offered among the different source grinds in its Our Certified lineup. The film also can be equipped with odor-absorbing technology, windows and easy-open features.
Sustainability points are scored because the all-film package weighs less than tray-based packaging, saving energy and reducing greenhouse gas emissions throughout the supply chain. Chubs also don’t need secondary packaging such as a carton or paperboard sleeve, another source reduction and environmental positive. On the downside, very little, if any, chub film is recycled. That could change as programs to recycle flexible packaging evolve. For example, chub packaging could play a role in resource recovery such as the Hefty EnergyBag Program, which collects non-recycled plastic waste to generate power. NP
Looking for a reprint of this article?
From high-res PDFs to custom plaques, order your copy today!