Cover Story
Case Farms: Worker Safety Success
Case Farms’ dedication to worker safety shines brightly through the operational improvements and low turnover rate at its Goldsboro, N.C., processing facility.
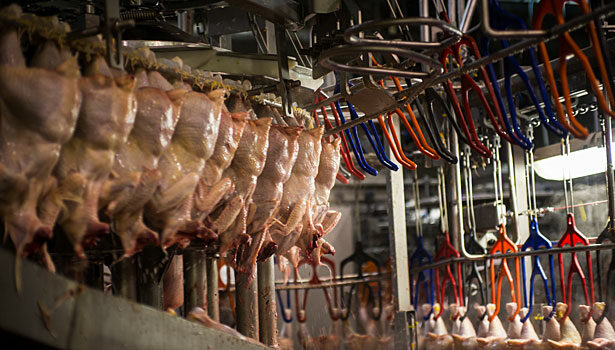

Andy Hanacek (left), editor-in-chief of The National Provisioner, and Brian Hanna, plant manager at Case Farms’ Goldsboro facility, discuss the newest equipment installed to improve worker ergonomics during the evisceration step.

Case Farms recently installed cutting equipment at the Goldsboro facility to automate the production of chicken strips and nuggets, improving worker safety on the floor. Whole-muscle breast pieces are lined up on a belt to be sent through the cutting machine (in these pictures, breasts are sliced into chicken strips), after which they are briefly inspected and sent on to packaging.

Case Farms recently installed cutting equipment at the Goldsboro facility to automate the production of chicken strips and nuggets, improving worker safety on the floor. Whole-muscle breast pieces are lined up on a belt to be sent through the cutting machine (in these pictures, breasts are sliced into chicken strips), after which they are briefly inspected and sent on to packaging.

Employees on the cone line have benefitted from installation of an automated wing splitter that allows them to cut the entire wing from the bird (this photo) and place it on a belt that takes it through the cutting apparatus (next photo). It’s another investment the facility has made to improve safety and ergonomics.

Employees on the cone line have benefitted from installation of an automated wing splitter that allows them to cut the entire wing from the bird (previous photo) and place it on a belt that takes it through the cutting apparatus (this photo). It’s another investment the facility has made to improve safety and ergonomics.








Take a job on the production floor of a meat or poultry plant, and you’re stepping into one of the most rigorous, demanding and physically draining positions you’ll ever hold.
Do you think Case Farms deserves to be the 2014 Plant of the Year? Vote for them in the National Provisioner 2014 Plant of the Year poll! |
No single processor has found the magic combination to put its production-floor jobs on any publication’s “top jobs” list yet. Nevertheless, processors who have put added focus on worker safety by investing in innovation have seen improvement in key workforce metrics as their employees feel as though their well-being is respected by management and important to company success.
Count vertically integrated chicken-processor Case Farms among those who have reaped the rewards of taking steps to better protect its workforce. To that end, Case Farms’ Goldsboro, N.C., facility has been recognized by the American Meat Institute and U.S. Poultry & Egg Association several times since 2012, and it stands as an example not only for its sister facilities at Case Farms, but the industry at large.
Solving problems by listening
Case Farms’ worker-safety success rides on the heels of dedicating itself to the cause from top to bottom, explains Case Farms’ director of human resources, Bobby Barragan.
“There are certain core elements of a worker-safety program that you really have to be strong on — they’ve got to be very well-polished,” he says. “One of the key elements is strong management commitment, and we have that from the very, very top.”
Many companies profess this to be the truth, but Brian Hanna, Goldsboro plant manager, says Case Farms has backed up its commitment with investment.
“When you have an owner [Thomas Shelton] who is committed to giving you the tools that you need to be successful, it’s passed on all the way down to the hourly employee,” he explains. “They know that if they say, ‘We need something here so we can do a better job,’ it’s not just going to be kicked to the curb. We’re going to listen, we’re going to review it, and if it’s feasible, it will be done.”
Barragan adds that employees throughout the company have learned that there’s no such thing as “crying ‘wolf’” at Case Farms. He says that at one of the company’s other facilities, maintenance spent an entire weekend relocating some equipment to a layout that the management believed would improve operations. However, the following Monday when the plant-floor employees returned to work, the setup wasn’t conducive to their operational needs, and they brought the complaint to management. After assessing the situation, the solution was simple, Barragan says.
“The next weekend, we fixed it — we could have said, ‘Live with it,’ but we didn’t,” he explains. “Even though it cost a lot of money to do it, we listened and did something about it, and the employees are happy with the latest setup.”
Hanna agrees, and filters the same mindset down through the Goldsboro plant.
“We can sit behind a computer all day long and come up with things that we need to do inside the plant, but if you don’t talk to the people that are actually doing the job, it isn’t going to work — you’ve got to make them part of the solution,” he says. “If it isn’t what they want and won’t make their lives easier, they’ll fight it tooth and nail.”
Securing the foundation
Alfredo Moreno, human-resources director for the entire Goldsboro Division, believes that commitment has given the company a strong base upon which to build a long-tenured workforce.
“Employee relationships get better and better once you commit to them, because they see that we’re here for their safety,” he says. “We preach that the way you come in to work is the way you need to be when you leave work to see your family. … The emphasis on safety trickles down, and we take it very seriously.”
Case Farms has been rewarded with loyalty — particularly at the Goldsboro facility. This summer, of all the employees scheduled to receive service awards for more than 10 years of employment at the company, roughly half of them work in the Goldsboro Division.
“When you have a facility with not a lot of turnover, you’ve got long-term employees who are used to doing those jobs,” Hanna adds. “You don’t have to bring in people off the street who haven’t worked for six months and then, all of a sudden, have to stand on their feet for eight hours and lift 40 pound boxes.”
Tenured workers don’t need the “work hardening” that new employees seemingly always struggle with when they start in a meat or poultry facility. In fact, Hanna says, it’s one of the misconceptions that the poultry industry needs to break through in order to retain workers, particularly in their first few weeks on the job.
“In the poultry industry, I think that’s one of the biggest contributing factors to so-called ‘injuries,’” he explains. “An employee has to [understand that] it’s like playing a sport: I haven’t shot a basketball in years, but if I go out there and play a game of basketball, I’m not going to be able to get out of bed in the morning.
“It’s not because I hurt myself, it’s just because I haven’t done it in a while, and I’m using muscles I’ve not used in years,” Hanna adds. “That’s what a lot of people don’t understand.”
Joanne Camacho, plant nurse for the Goldsboro facility, says that Case Farms makes new employees very aware of the difference between being “sore” and being “injured” on the job.
“When we hire people, that’s the first thing we tell them: ‘Expect to be sore,’” she says. “We give them exercises, stretches to help minimize the soreness. You can’t force them to do it, … but we’ve done pretty well with not having a whole lot of musculoskeletal problems.”
Training and prevention
To further involvement of the employees in the safety program, Case Farms has developed specific training departments at each facility, and the Goldsboro team has instituted weekly hazard-prevention walk-throughs that involve Hanna, the safety manager, the maintenance manager and each individual departmental manager.
According to Barragan, the training department has made a difference in getting employees involved. He says that the company developed the concept in August 2012 to be fine-tuned at each individual location, but members would report up through the corporate training portion of the organization tree, not the operations branch.
“We would guide them through the process until they graduated,” Barragan says. “Then they’d get a certificate — we’d make a big deal out of it and also give them a bump up in pay before their scheduled increase. To be graduated, they had to show the trainer and the receiving supervisor that they could do the job safely and with quality.”
Since the start of the program, 828 employees have graduated company-wide, with 237 working on their certificates at presstime.
Goldsboro’s hazard-prevention program furthers the mantra of keeping the lines of communication open, but it also helps catch the finer details needed to maintain efficiency, safety and operational excellence. Hanna says that, as in any job, day-to-day repetition can create a “blind spot” to minor issues because of a focus on bigger-picture issues.
“I tell my supervisors this all the time — they get so caught up in running chickens that they forget how to run chickens,” he says. A line supervisor or worker looks at his or her area all day long, every day, so slight changes aren’t always immediately evident, because that employee is focused on overall goals. To make sure those minor details aren’t missed, Hanna says, the Goldsboro plant brings employees from other departments in for the safety walk-throughs.
These walk-throughs handle the minor issues that arise across a variety of operational demands, but Case Farms’ quarterly worker-safety audits truly put a fresh set of eyes on each facility, with an intent focus on being proactive toward protecting its workforce.
All of Case Farms’ safety managers participate, traveling to each facility and going through them in a couple days with a fine-tooth comb to find potential issues and create solutions. Barragan says the program, which was started in 2010, succeeds because of the diverse manufacturing background of the safety managers at each facility.
“At the beginning of each year, as I visit the locations, we go over last year’s results,” he says. “I share the results, and each complex gets to see how they’re doing against their sister facilities, because a little competition is always good.”
Barragan sees the results first-hand when comparing the facilities, and states that Goldsboro may be the company-leading facility at the moment, but the others are quickly making up ground, inspired by the success of others in the company. The Canton facility, he states, had an atrocious worker-safety record in 2012, the year Case Farms acquired it, before it stepped up its efforts and reversed direction. To that end, at presstime in early April, the facility still had yet to register a single OSHA recordable injury in 2014.
Shielding the investment
In Goldsboro, the audits and walk-throughs have allowed for capital investment that has helped take the employees out of harm’s way, while still upholding the quality standards of Case Farms’ customers.
Removing some of the jobs that require repetitive motion and eliminating some employees’ need to handle and use sharp tools has definitely made a difference in the realm of worker safety, according to Hanna.
“As new technology comes along, the machines get faster and better, and they make better cuts,” he adds. “In trying to lower your injury rates, you [need to] take the approach of, ‘What can we do to allow you to work safer and more efficiently?’ Efficiency and safety go hand-in-hand.”
In the past year and a half, Case Farms’ Goldsboro facility has invested in a variety of capital improvements, including a new evisceration line, new cutting equipment and pallet jacks and forklifts — each bringing efficiency, quality and safety improvements to the table.
Hanna explains that the new evisceration line makes the cuts that three employees would have had to make in the past, and even though Case Farms rotated workers through, repetitive-motion injuries were a concern. Now, one employee supervises the equipment to ensure optimum operation, and the others have moved on to safer tasks in the facility.
Further along the processing line, Goldsboro used to manually slice whole-muscle chicken strips and nuggets, until it invested in equipment that does the work consistently and efficiently enough to take the knives out of the hands of the employees. Also, Goldsboro invested in automatic wing splitting equipment, removing another cutting step from employees’ task lists.
It should be no surprise that Hanna and his team have a “to do” list already in the works. Hanna expects to upgrade several areas in the near future, including areas where he believes more cutting tasks can be transitioned from manual tasks to automation. Additionally, Goldsboro plans to renovate its box-assembly operation, installing new box machines, chutes and conveyor belts to eliminate the manual labor required to move materials and assembled boxes, as well as the inherent hazards involved in having pallets, pallet jacks and materials that need to be carried.
Improvements aren’t limited to operations, however. Camacho reports that, after nearly 14 years working in occupational health, she’s made it her mission to revamp the Goldsboro plant’s accident investigation form.
“I want to get to something that’s more in-depth and thorough, but also easier [than what we have], maybe using checkboxes, for example,” she says. “That way, the supervisors and employees don’t have to write a whole lot of explanation about what happened. Everyone would mark checkboxes.”
Moreno says that whatever the Goldsboro processing facility uses in its strategic approach to worker safety, the message needs to be communicated across all the divisions of the vertically integrated company.
“We need to tackle the fact that some don’t always get the message that, it doesn’t matter how minimal an injury seems — those near-miss injuries too — we have nurses 24/7 here,” he says. “Sometimes, though, they forget, or they say, ‘I’ll be fine,’ and it gets worse later. So we need to advocate that they let us know immediately.”
As processors such as Case Farms raise the bar for the rest of the industry by demonstrating how investment in the protection of their workers produces loyalty, which in turn improves the bottom line by maintaining the high quality of products, smart processors will follow suit and begin to serve and protect their workforce.
Looking for a reprint of this article?
From high-res PDFs to custom plaques, order your copy today!