Farm to Plate: A systematic approach
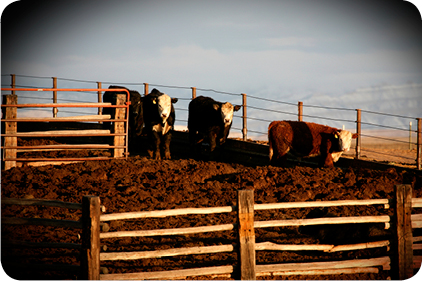
Last September, the Food Safety and Inspection Service issued Directive 6900.2 Revision 2. A significant portion of this directive was focused on recommendations for the development of a robust systematic approach to animal welfare for slaughter establishments. Many larger plants were already operating under their own systematic approaches when the directive was released. As a matter of fact, a strong argument can be made that the industry’s initiative to develop the systematic approach to animal welfare prompted FSIS’s recommendation.
Since the advent of HACCP in the meat industry in the 1990s, many companies have realized the strength of HACCP as a management tool and applied its principles to other areas of their production facilities. The systematic approach to animal welfare is the HACCP plan for animal welfare in livestock slaughter facilities.
In January, I offered a course at the University of Wisconsin-River Falls that led undergraduate animal-science students through the seven principles of HACCP, the development of a systematic approach to animal welfare for a commercial slaughter facility, and on-site installation of the program.
At the beginning of the development process for the systematic approach, we identified the guidelines, regulations, and other documents that would be important in shaping the critical control points (CCPs) and standard operating procedures (SOPs), which make up a significant portion of a HACCP plan. An excellent starting point for the systematic approach development process in most red-meat slaughter facilities is 9 CFR 313 and the American Meat Institute’s Guidelines on the Care and Handling of Livestock.
As the critical limits (CLs) were developed, we turned to peer-reviewed scientific literature whenever we could. Finding supporting documentation for the unloading, lairage and stunning procedures is challenging because the body of useful literature is still small in this area. Fortunately, there has been considerable effort on the part of meat and animal scientists to fill this void in the literature in recent years.
Before we started drafting the SOPs, CCPs and CLs, we recorded and reviewed a video of the typical animal movement through the plant from unloading, through stunning, and onto the bleed rail. This video helped us to develop a process flowchart for the systematic approach that was synchronous with the actual flow of animals through the plant.
During the development process, we watched the video twice. First, we watched the entire video without stopping to gain a full view of the process. Next, we watched the video again but stopped it at each step in the process flow as we constructed our flowchart. This is also a good time to list the potential SOPs and CCPs at each step. After the process flowchart was complete, we watched the entire video again and confirmed that our process flowchart was an exact match.
One of the challenges in designing a HACCP plan can be making the differentiation between a CCP and an SOP. The important point to remember is that a CCP is a critical control point — it includes a clearly defined critical limit that will result in process failure if there is a noncompliance. An SOP is a detailed description of a process that is performed the same way every time.
The CCPs are the points in the process where some form of testing or assessment occurs, and failure (which is defined by the critical limit) results in process stoppage followed by corrective action. For our systematic approach to animal welfare, we relied heavily on 9 CFR 313 to guide us in the determination of CCPs and CLs. The rationale behind this decision was that a violation of some portions of 9 CFR 313 will result in immediate suspension of pre-slaughter handling and/or stunning operations.
As an example, if an animal returns to consciousness after stunning and it has been shackled and hoisted, the plant has violated the sections of 9 CFR 313 that require all animals to remain unconscious during the casting, shackling, hoisting, bleeding and slaughter procedures.
After spending a week in the classroom to design and build the systematic approach for our collaborating plant, we traveled to the facility to install the new program. The time we spent building the program outside of the actual production facility was important, because it allowed us to be well-prepared to install the program. One of the keys to a successful implementation of a new program is preparation.
Before we jumped into installing the log forms and training the handling and stunning personnel at the plant, we performed multiple program walkthroughs — first in the empty facility before production started, then during production. This allowed us to identify any major issues with process flow and assignments of CCPs.
After we were confident that the program matched the process flow in the plant, we tested all log forms and monitoring procedures in the program. This step is very important in the survival of a new systematic approach to animal welfare.
Since such a program is not mandated by the FSIS at this time, there is no rush in defining an official installation date. I recommend that a brand new systematic approach is test-run for at least several days before an official installation date is identified. The rationale behind this is that if a critical limit was not set appropriately or a monitoring procedure is too labor-intensive and requires streamlining, these changes can be made before the program is officially installed. After the program has been officially installed, FSIS personnel expect a facility to follow their program. Make sure the program works well before you officially install it.
The final step in the installation process was the training of plant personnel. This included the quality-assurance personnel that were responsible for training and monitoring the performance of handling and stunning personnel, the stunner operators and handling personnel, and key members of plant management.
We constructed training programs that matched the content of the new systematic approach for the plant. We also included pictures and terminology that came directly from the facility — this helps to improve the application of the training material. Over the years, many training programs in many industries have relied on videotapes of training sessions that appear outdated or outside of the scope of the operation. It is difficult for an employee to take a training program seriously if it appears that management is just “going through the motions” by throwing a training video in the VCR and walking away for 30 minutes.
The development of a robust systematic approach to animal welfare is an important piece in maintaining consistent performance in the humane handling and stunning of livestock. It is not a small task, but the rewards of a robust systematic approach and training program are worth the investment.
A well-built program serves to maintain employee accountability, animal well-being and, ultimately, consumer trust. But you must stay committed to the program.
If you spend the time to build it and install it, but it is printed off, snapped into a binder and placed on the shelf to collect dust until your next humane-handling audit, you are not getting sufficient return on your time investment in building the program. Start simple and let the program evolve over time.
Looking for a reprint of this article?
From high-res PDFs to custom plaques, order your copy today!