Emission Control
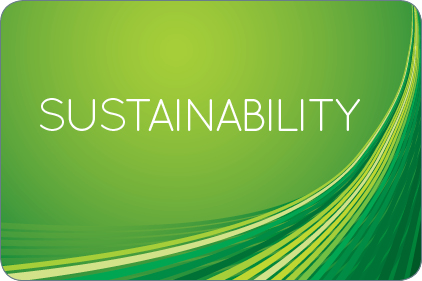

The meat and poultry industry is committed to ensuring a safe food product for our customers, maintaining the highest animal-welfare standards for our livestock, providing a safe and rewarding work environment to our employees, reaching out to the communities in which we do business, and working to minimize our environmental impact. The industry continues to make improvements in all of these areas with the help of science, research and technology. Short and long-term goals of the meat and poultry industry include focusing on our local, national and global environmental impact, and finding ways to minimize this impact through energy and water conservation, enhanced recycling and waste minimization practices.
In terms of the meat and poultry industry’s environmental impact, the industry is continuously working to deploy technologies, like filters and scrubbers, to reduce or remove the potential pollutants from any air or water stream exiting the facility. These plant emission controls are critical not only to comply with state and federal regulations, but to improve facility efficiency and to maintain a healthy environment for everyone who works in and around the facility. The most significant pollutants our industry faces include, but are not limited to, odors, particulate matter, sulfur oxides from fuel combustion, hydrogen sulfide in biogas and nitrous oxides from boilers.
To have an emission control system means that the pollutant of concern is amenable to reduction or removal, which can prove challenging depending on the pollutant. Odor-causing compounds include volatile organic compounds (VOCs) and many nitrogen and sulfur compounds, as well. Due to the hydrophobic properties of VOCs, unlike the readily water soluble nitrogen and sulfur compounds, VOCs must be removed from air streams using different technologies. Through the use of vapor phase activated carbon, VOCs are physically adsorbed to activated carbon, leaving VOCs in the exiting airflow virtually non-detectable. Additionally VOCs can be removed from the air using thermal incinerators, which can have a 99.9% destructive efficiency. The hydrophilic nitrogen and sulfur compounds can be scrubbed using a variety of chemical solutions.
Particulate matter from the rendering process, e.g., fats and oils, carry odors as well and can be scrubbed with water and odors removed via a heat exchanger or filtered using fabric filters that separate these particles into dust collectors (known as a baghouse). Fine particulate matter such as oil mists can be collected using electrostatic precipitation (ESP), which uses electrostatic charges to separate the particulate matter from the air stream that passes between electrodes. Fine dry dust, however, is best removed using a baghouse, which also allows a company to recycle what is captured.
For facilities using direct fired processes, such as smokehouses or rendering dryers, sulfur oxides from fuel combustion should be addressed. These can be controlled through methods similar to those used to address odors. There are various sulfur-scavenging compounds available for controlling hydrogen sulfide in biogas, which have been developed for the oil industry, along with an oxidative bacterial process. Finally, emissions from boilers including greenhouse gases (GHG), especially nitrous oxide, are another challenge that can be addressed through the use of low-nitrous oxide burners and fine-tuning boilers to improve overall efficiency. Many facilities are installing stack economizers and/or heat recovery units on their boiler stacks. The heat recovery units are used to transfer heat to a water source, which minimizes the energetic pull on a water heater.
Looking forward, the new policies on GHG emissions will present a significant opportunity for emission reduction throughout not only the meat and poultry industry, but across a vast array of manufacturing industries. With the implementation of specific, best-available control technologies, facilities can work to reduce GHG emissions, thereby minimizing their environmental footprint and complying with government regulations.
Emission control systems are used throughout the industry as ways to improve the overall efficiency of a system, comply with state and federal regulations, and meet reduction goals set by the company. The industry is committed to reducing its environmental footprint through energy and water conservation practices, enhanced recycling practices, and waste minimization strategies. The meat and poultry industry is proud of the accomplishments it has made not only in the environmental arena but also with respect to food safety, animal welfare, worker safety and community outreach.
For more information, visit www.sustainablemeatindustry.org.
Looking for a reprint of this article?
From high-res PDFs to custom plaques, order your copy today!