Spare Parts Know-How
Three questions to ask before standardizing your spare parts program
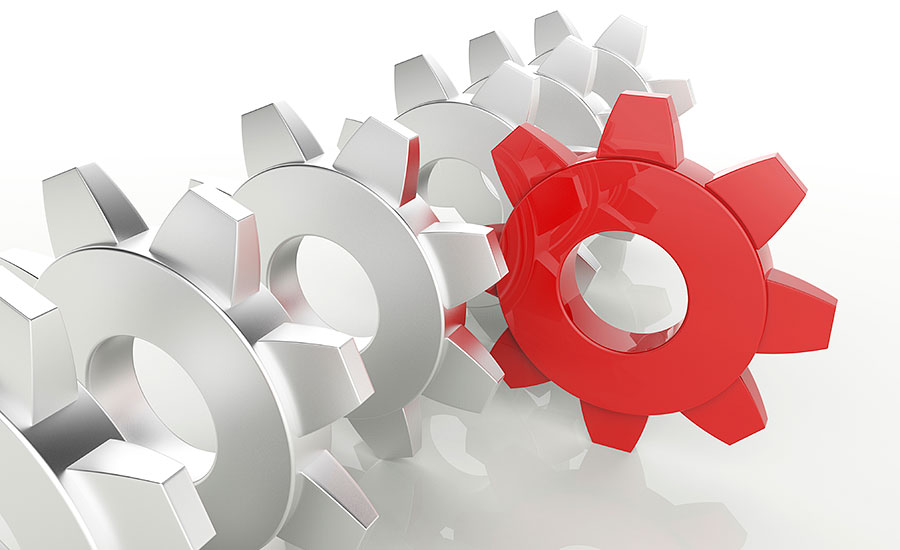
Whether to standardize equipment and spare parts is one of the enduring debates of engineering, maintenance and spare parts management. On the one hand, standardization is said to lead to improved operating and manpower efficiency, as well as reduced inventories. On the other hand, not standardizing is said to enable companies to take advantage of technical developments and innovation. One thing that is certain is that the impact of explicit pros and cons are hard to quantify and will be specific to the individual circumstance.
First, let’s define standardization. The Merriam-Webster online dictionary suggests a simple definition of standardize as “to change things so that they are similar and consistent and agree with rules about what is proper and acceptable.”
Standardizing for spare parts management usually means agreeing that a certain type/model of equipment will be used and with that the spare parts required for each installation will be the same.
The pros and cons of standardization
So just what are the pros and cons of standardization? Here are the most commonly cited:
Pros
- Fewer parts to manage
- Lower inventories
- Operational familiarity
- Improved maintenance efficiencies
- Improved purchasing efficiencies
- Fewer invoices to process
- Lower parts costs
Cons
- Missed innovation
- Reduced operational efficiency
- Increased obsolescence risk
- Increased parts costs
- The perceived risk of using non-OEM parts
This list demonstrates why the arguments for and against standardization are not straightforward: One of the pros is the potential for reduced parts costs and one of the cons is the potential for increased parts costs. How can both arguments be true? It all depends on the specific circumstance.
Questions to consider
In deciding whether to standardize on a particular type/model of equipment and the associated spare parts, a detailed examination of the specific circumstance needs to be completed. This will include determining the real impact on your company of any change of policy and ensuring that the motivation for ordering non-standard equipment is justified. These are the three key questions to ask:
- Is there a genuine innovation/operational advantage?
- How much more/less inventory is required and what does that cost/save?
- If a change in type/model is agreed, is there a way to gradually move to the new type/model as the old ones are used up (meaning that the old type/model will no longer be ordered)?
When working through the standardization decision, be mindful of the motivation. Is it because someone just wants the latest thing? (Some might call this the “cool factor.”) Is it motivated by vendor bias? (A preference for, or dislike of, a specific vendor.) Is it motivated by a perception of quality for high-priced components? (Sometimes referred to as “gold plating.”)
Standardization is not trivial. At a minimum, it requires a quantification of the costs or savings that might arise and an assessment of the associated risks. Like all management and investment decisions relating to spare parts holdings, it is not simply an engineering, operations, storeroom or procurement decision, but the result of the consideration of all functions that are involved. NP
Looking for a reprint of this article?
From high-res PDFs to custom plaques, order your copy today!